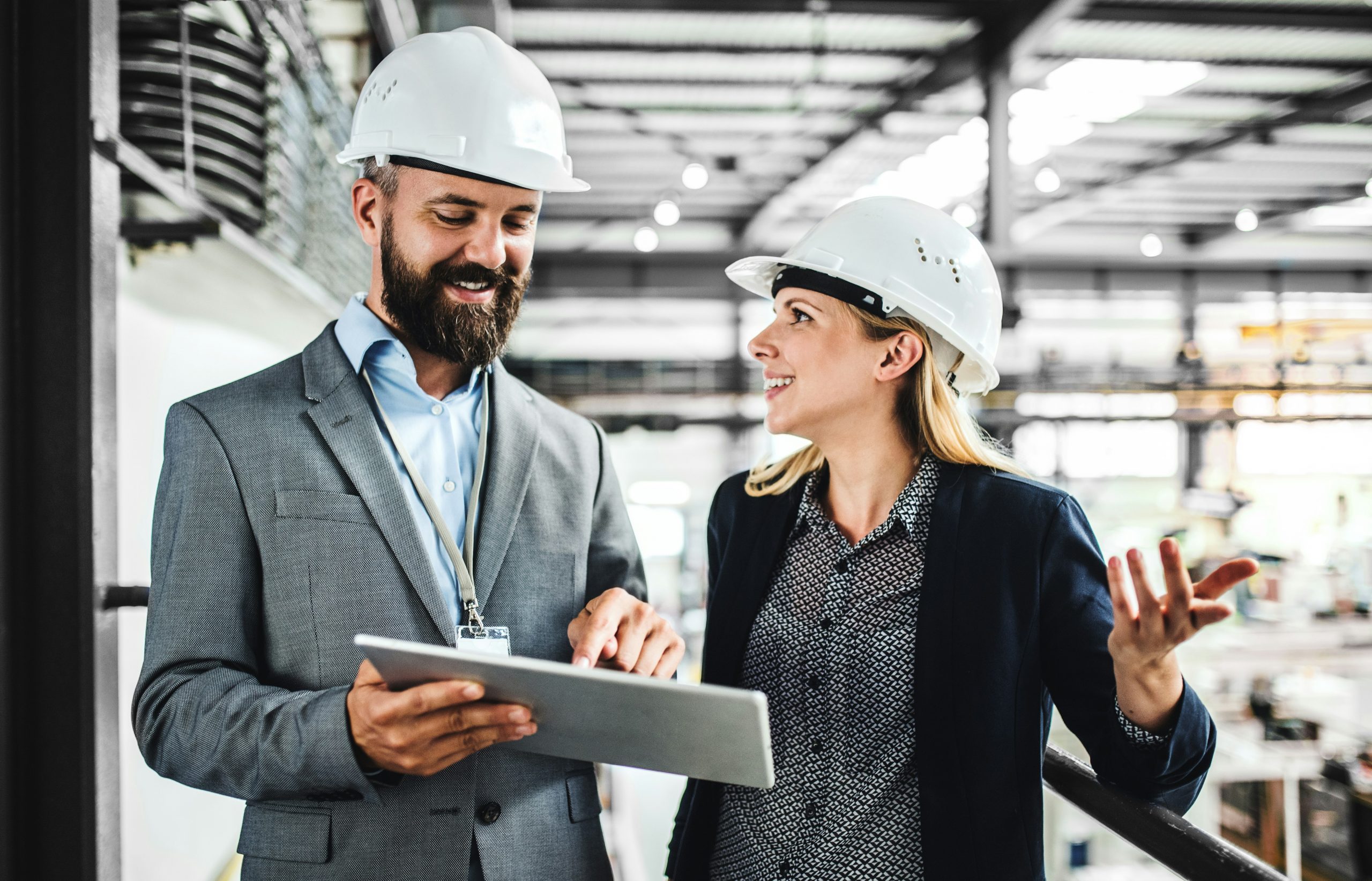
A manufatura enxuta, ou Lean Manufacturing, tornou-se um conceito fundamental no mundo industrial moderno. Com foco na eliminação de desperdícios, aumento da eficiência e melhoria contínua, a abordagem busca transformar os processos de produção de forma que cada passo agregue valor. Isso envolve a constante revisão de métodos, ferramentas e práticas para criar um fluxo de trabalho mais eficiente e eficaz. Entre os especialistas que se destacam nesse campo, estão os líderes reconhecidos como autoridades em melhoria contínua. Esses profissionais dedicam suas carreiras a otimizar a produção e a fomentar uma cultura de aprimoramento constante.
A Essência da Melhoria Contínua
A melhoria contínua, ou “Kaizen”, é um conceito central no Lean Manufacturing. O termo japonês “Kaizen” significa “mudança para melhor” e envolve um processo constante de pequenos ajustes que visam melhorias progressivas. Para as empresas que adotam este conceito, a melhoria contínua não é vista como um evento único ou uma atividade isolada. Ela é uma prática constante e cultural, onde todos os funcionários, desde a linha de frente até a alta gestão, são incentivados a buscar maneiras de melhorar os processos de trabalho. A ideia é que cada colaborador, independentemente de sua função, possa identificar problemas e propor soluções para aumentar a eficiência e reduzir desperdícios.
Essa abordagem é sustentada por várias ferramentas e técnicas, como o ciclo PDCA (Plan, Do, Check, Act), que promove um método estruturado de resolução de problemas. Ao aplicar o PDCA, as organizações podem revisar continuamente suas operações, identificar áreas de melhoria e implementar soluções de forma controlada.
O Papel dos Especialistas em Melhoria Contínua
A autoridade em melhoria contínua na manufatura enxuta é um papel altamente especializado. Esses profissionais são responsáveis por liderar as iniciativas de aprimoramento dentro de uma organização. Eles atuam como facilitadores de mudanças, guiando as equipes para entender e aplicar os princípios do Lean. Isso envolve treinamento, mentoria e, muitas vezes, a implementação de sistemas de gestão da qualidade. Além disso, esses especialistas são fundamentais na adaptação das práticas de Lean às particularidades de cada empresa.
Para se tornar uma autoridade em melhoria contínua, um profissional precisa ter um profundo entendimento das metodologias Lean e dos principais indicadores de desempenho. A experiência prática é igualmente importante, pois permite ao especialista identificar problemas reais e desenvolver soluções eficazes para a operação. A certificação em Six Sigma ou Lean, bem como a experiência em implementação de processos Kaizen, são qualificações comuns para esses especialistas.
Implementação do Lean Manufacturing nas Organizações
A implementação de Lean Manufacturing em uma organização exige mais do que apenas o treinamento da equipe. É necessário um compromisso de longo prazo com a cultura de melhoria contínua e a disposição para adaptar todos os processos de produção. O primeiro passo é identificar as áreas de desperdício, que podem incluir tempo, recursos e energia. As ferramentas Lean, como o mapeamento do fluxo de valor e os 5S, ajudam a visualizar e eliminar esses desperdícios de forma sistemática.
Uma vez identificados os desperdícios, é possível aplicar técnicas específicas para eliminá-los. O uso de ferramentas como o Just-in-Time (JIT) e o Kanban pode otimizar a gestão de estoques e a programação da produção. O Kaizen, com sua ênfase em pequenas mudanças contínuas, também se aplica na identificação e eliminação de desperdícios ao longo do tempo.
Além disso, a implementação de Lean exige um envolvimento constante da liderança. Os gestores precisam ser os primeiros a adotar e promover as práticas de melhoria contínua. Eles devem criar um ambiente que incentive a colaboração e o compartilhamento de ideias entre os membros da equipe. Isso pode ser alcançado por meio de reuniões regulares, workshops e treinamentos, que ajudam a manter o foco no aprimoramento contínuo.
Benefícios da Melhoria Contínua no Contexto Lean
Adotar uma abordagem de melhoria contínua dentro do Lean Manufacturing traz diversos benefícios tangíveis e intangíveis para as organizações. Um dos principais benefícios é o aumento da eficiência. Ao eliminar desperdícios e melhorar os processos, as empresas podem produzir mais com menos recursos. Isso não apenas melhora a produtividade, mas também reduz os custos operacionais, o que pode resultar em maiores lucros e um melhor posicionamento competitivo no mercado.
Outro benefício importante é a melhoria da qualidade. Como o foco do Lean é minimizar os erros e problemas, a qualidade do produto final tende a aumentar. Isso ocorre porque os processos são constantemente analisados e ajustados para evitar falhas e reduzir a variabilidade. Com menos defeitos e retrabalho, as empresas podem entregar produtos de maior qualidade, o que aumenta a satisfação do cliente e reforça a fidelidade à marca.
Além disso, a melhoria contínua promove um ambiente de trabalho mais positivo e colaborativo. A cultura de melhoria contínua incentiva todos os funcionários a se envolverem no processo de mudança, criando uma sensação de pertencimento e realização. Isso não só melhora a moral da equipe, mas também ajuda a desenvolver uma força de trabalho mais qualificada e engajada.
Desafios e Soluções na Implementação de Lean
Apesar de todos os benefícios, a implementação do Lean Manufacturing e da melhoria contínua não está isenta de desafios. Um dos maiores obstáculos é a resistência à mudança. Em muitas organizações, os funcionários podem se sentir desconfortáveis com as novas práticas ou duvidar da eficácia das abordagens Lean. Para superar isso, é essencial que a liderança se envolva ativamente no processo e comunique claramente os benefícios da mudança. Treinamentos regulares e a criação de uma cultura de aprendizado contínuo também são fundamentais para superar a resistência.
Outro desafio é a manutenção da consistência ao longo do tempo. A melhoria contínua é uma jornada, e os resultados não são imediatos. Organizações podem ficar desmotivadas se não virem resultados rápidos, o que pode prejudicar o comprometimento a longo prazo. A solução aqui é definir metas claras e alcançáveis, medindo o progresso de maneira contínua e celebrando as vitórias, por menores que sejam.